You are Here: Process Software >> Process Improvement Techniques
Shuri wants to improve a few processes in her office that have caused delays and inefficiencies at the workplace. They worked fine when the company was small, but now they can’t handle the load anymore. Shuri needs to analyze where the bottlenecks are, and find ways to improve them. Hence, she needs to choose the right process improvement technique.
So, What Exactly is Process Improvement?
Process improvement is a simple yet powerful idea. It is how businesses identify the parts of their business processes where they can increase their profit margins, cut down on expenditures, and speed up their operational timelines.
It’s not a radical or new concept–it was introduced by James Harrington as early on as 1991–but it’s especially important today.
There are a lot of methods and techniques through which a company identifies problem areas in their business processes. These process improvement techniques can analyze not only processes, but also design improvements that can help scale processes once the business grows larger.
Why You Need Process Improvement Today
Processes that run like clockwork can breathe life into your business (and profits), and ineffective processes can go so far as to kill your company. Even Bill Gates’ rule of thumb states that “A lousy process will consume ten times as many hours as the work itself requires.”
Inefficient processes lead to a waste of precious employees’ time
- The time that someone spends doing an unnecessary and redundant task could’ve been better spent in more valuable areas.
Working standards can drop
- Inefficiently built processes often mean that work becomes defective. Reports can go missing, deadlines can be missed, and employees can drop the ball in so many areas.
Productivity can take a hit
- The bottom line in any business is the finances, and productivity losses first hit this vital area. If you’re paying a team to do a job that could be easily automated, you’re literally losing money by the minute.
Besides these reasons, you’ll also want to stay ahead of radical improvements in technology, industry trends, and how your competition operates.
How Process Improvement Works
Business Process Improvement can work in two ways: it can flow through a structured path, or take a more informal route. Either way, though, it tends to follow four common steps.
1. Process Audits, And Finding Improvement Opportunities
- The audit is usually the best place to start process improvement efforts. Here’s what you should be looking for: opportunities to improve process, and potential risk areas. This will help you strategize business improvement, especially in regard to prioritizing specific areas.
- At this stage, it’s a good idea to get an understanding of how tweaking a particular process will impact resources, as well as stakeholders–which may be the organization itself, teams, individual employees, partner organizations, vendors, or customers.
2. Analyze Process That Are Currently in Use
- Once you’ve established which area you want to improve, spend time analyzing the processes that are in place. You can do this through process mapping (workflows), cause/effect studies, and operational surveys.
- Ask the right questions: Check if the process is broken, and where. Which steps cause delays/bottlenecks, and which ones are costly? Which steps cause quality losses?
3. Build Commitment and Support
- A commonly skipped step, and often the difference between a token effort and one that brings real change.
- Process improvement isn’t an instant do-over. It requires a dedicated commitment across the board, and that’s why getting senior management support is crucial. Managerial support will make the difference when you explain the change in the status quo, and why it is necessary.
- Improving processes takes a lot of time and resources, so make sure you get the all-important upper management approval and support.
4. Strategize Your Process Improvement Plan
- A good strategy will include the steps you’ve isolated as problem areas, why they are problem areas, and how you plan to improve them. Make sure that your process improvement objectives are realistic, measurable, and necessary in the context of your organization’s strategic long-term and short-term goals.
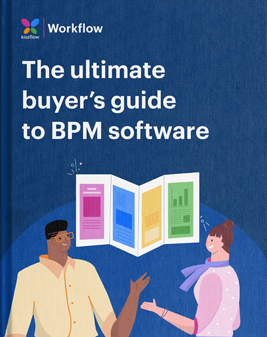
#Free eBook
The Ultimate Buyers guide to BPM Software
Thank you for Showing Interest
Our Team will contact you soon
Process Improvement Techniques:
Here are the 5 Process Improvement techniques:
- Process Maps
- Fishbone Diagrams
- Histogram Charts
- Scatter Diagrams
- Pareto Chart
The choice of process improvement technique is entirely dependent on the scope of improvement in the project. In each description, you’ll find a recommendation of where each one works best.
1. Process Maps
Also commonly called flowcharts, these diagrams are used to visually represent relationships and tasks that make up a process. In a process map, you typically start from the top and move downward, working from the initial task to the final one.
From the higher levels, you can get an understanding of the complexity of the process, thus ensuring that you have a macroscopic understanding of how the process works. At the bottom level, you’ll gain an understanding of how each individual task plays a part in the process.
Using a process map, you can easily chart out a complex process diagram to give you and your team clarity on how the process improvement will work.
Process maps are great when you’re designing actual processes on products like Kissflow Process, since these process maps can effectively be translated into real and applicable processes into the software.
2. Fishbone Diagrams
Fishbone diagrams are also known as Cause and Effect diagrams or Ishikawa diagrams. They’re techniques in determining problems and how they arise in a process. Typically done at the beginning of a Root Cause Analysis, fishbone diagrams help in finding out where a problem is and organizing the causes for a problem. This can include the people working on it, the methods that are used, the equipment that is currently used in the existing process, and the environment the process is running in.
Using the data that is gathered from this diagram, you can find out where a process is faulty or underperforming, and see where you need to make appropriate changes for process improvement.
Fishbone diagrams are a great tool for business process improvement, since they can be done entirely offline, and help teams that are working on process improvement find the core reason the process isn’t performing as required, or where the improvement needs to be done.
3. Histogram Charts
Histogram charts are another technique at your disposal when trying to make process improvement. They show the relationship of data between a variety of variables over time. This is particularly useful if you’re doing process improvement analysis.
You can find out how the process was performing at its peak. Using that, you can change different variables to see what was the cause for the performance increase, and alternatively, see what was the detriment to any performance decreases, and make note of the same for your process improvement.
Histogram charts don’t point out which part of the process needs improvement, but they’re useful in finding out which variables affect the performance. Using this, small changes can be made.
4. Scatter Diagrams
Scatter diagrams are another technique in process improvement analysis. They use current variables to establish the current pattern, and predicted variables to see how the process will perform. This is useful since you can see which changes give outcomes that are favorable, and avoid any changes that seem to give negative outputs.
Scatter diagrams are used in hypothesis testing. This helps you see if there is a direct correlation between variables and the end impact on performance. If the scattering is close together, it indicates a higher correlation. If the scattering is further apart, that indicates less correlation.
5. Pareto Chart
A Pareto chart is a ranking of defects, causes, and/or data in a process. They’re ranked from the most significant to the least significant. This kind of ranking helps in process improvement analysis, since you can filter out the major factors that need attention and the details that don’t affect the process much.
Using this data, you can channel your efforts into focusing on those factors that cause the greatest impact, while leaving the smaller details for a later time.
Conclusion
Process improvement techniques are great at revealing weaknesses in existing processes, and finding ways to scale up processes or remove operating flaws altogether. Using a software like Kissflow Process, you can effectively analyze your process and figure out the strong points are, and what needs to be improved. That data can help you focus on improving your process, without having to create something from scratch.
If you ever find Shuri mumbling to herself and muttering “bottlenecks and processes” under her breath, you know what to suggest!